Predictive Maintenance
Predictive Maintenance Definition
Predictive maintenance refers to the use of data-driven, proactive maintenance methods that are designed to analyze the condition of equipment and help predict when maintenance should be performed.
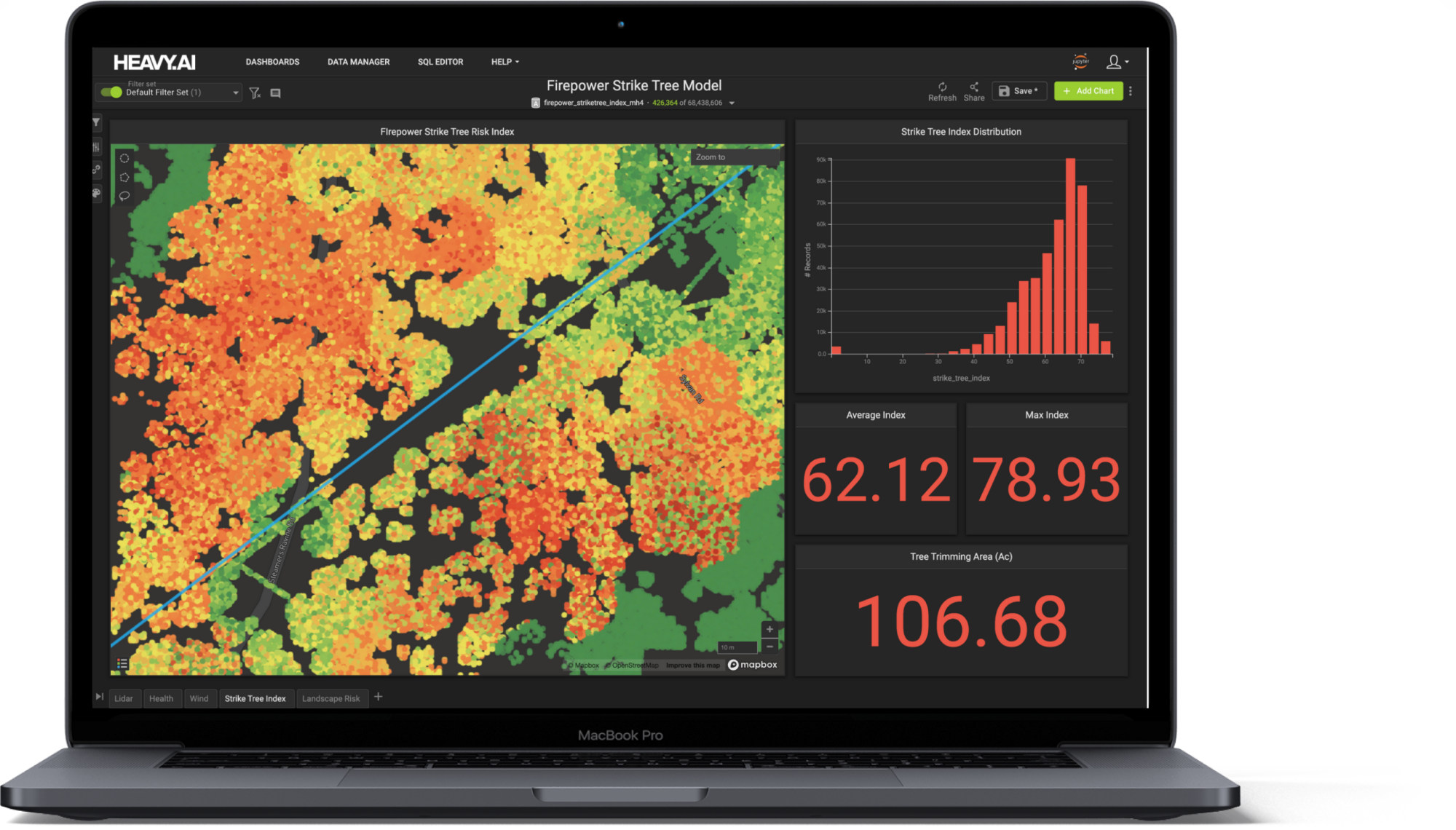
FAQs
What is Predictive Maintenance?
Predictive maintenance software uses data science and predictive analytics to estimate when a piece of equipment might fail so that corrective maintenance can be scheduled before the point of failure. The goal is to schedule maintenance at the most convenient and most cost-efficient moment, allowing equipment’s lifespan to be optimized to its fullest, but before the equipment has been compromised.
The underlying architecture of predictive maintenance solutions typically consist of data acquisition and storage, data transformation, condition monitoring, asset health evaluation, prognostics, decision support system, and a human interface layer.
Predictive maintenance technologies include nondestructive testing methods such as acoustic, corona detection, infrared, oil analysis, sound level measurements, vibration analysis, and thermal imaging predictive maintenance, which measure and gather operations and equipment real-time data via wireless sensor networks. Predictive maintenance solution providers utilize these measurements and predictive maintenance machine learning techniques, such as the classification approach or the regression approach, to identify equipment vulnerabilities.
The predictive maintenance process flow consists of the following steps:
- Determine equipment and failure mode to be monitored.
- Establish frequency.
- Monitor condition.
- Issue report.
- Is there an abnormality? If no, return to Step 3. If yes, continue to Step 6.
- Create work order.
- Plan work date.
- Ensure parts and labor are available.
- Perform repair.
- Close work order and return to Step 3.
Preventive vs Predictive Maintenance
The difference between preventive maintenance and predictive maintenance lies in the data being analyzed. While a predictive maintenance technician relies on monitoring and analyzing data from the actual, current condition of the equipment in operation, preventive maintenance relies on historical data, averages, and life expectancy statistics to predict when maintenance activities will be required.
Corrective maintenance refers to the actual repair or replacement of equipment that has malfunctioned, broken, or worn down. The corrective type of maintenance is known as reactive maintenance. Preventive, predictive, and corrective maintenance are especially crucial for safe operations in the Oil and Gas, Manufacturing, Telecommunications, and Railway industries.
How to Implement Predictive Maintenance
Manufacturers are increasingly using Internet of Things (IoT) predictive maintenance and AI predictive maintenance services to implement automatic predictive maintenance in their operations and equipment. Predictive maintenance software companies provide predictive maintenance products, predictive maintenance services, and system integration services.
AI in predictive maintenance can tailor maintenance routines to the needs of each individual piece of equipment, can be trained to visually identify flaws and patterns in equipment, can follow Computer Aided Design instructions without additional system programming, and can use algorithms to optimize supply chains in an ever-fluctuating market. Automatic detection of anomalies reduces unplanned downtime and costs by quickly providing an estimate for when equipment will fail.
The steps to implement a predictive maintenance program generally include: identify critical assets, establish a database for historical data, analyze failure modes, make failure predictions, then deploy the predictive maintenance technology to a group of pilot equipment to validate the program.
Condition Based Monitoring vs Predictive Maintenance
Condition based monitoring is a type of predictive maintenance that relies on sensor data, such as vibration monitoring systems, to measure the condition of equipment over time while it is in operation. Maintenance is only performed when the dataset for predictive maintenance indicates that performance has decreased or a failure is likely.
Why Predictive Maintenance is Important
Predictive maintenance insights are an extremely valuable asset in improving the overall maintenance and reliability of an operation. Benefits include:
- minimize the number of unexpected breakdowns
- maximize asset uptime and improve asset reliability
- reduce operational costs by performing maintenance only when necessary
- maximize production hours
- improve safety
- streamline maintenance costs through reduced equipment, inventory costs, and labor.
Does HEAVY.AI Offer a Predictive Maintenance Solution?
Predictive maintenance implementations are responsible for efficiently planning and predicting the faults of devices throughout the Public Sector, Telecommunications and Oil & Gas industries. Both sectors consist of components that are highly suitable for machine learning use cases.
Enormous volumes of data are gathered and stored from Telco devices, giving operation teams the opportunity to respond to failures before they occur. Replacement parts can be organized according to alarm predictions, and the actual number of alarms can be mitigated by preventing them before they occur. Similarly, big data generated from Oil & Gas devices can be leveraged to improve yields and reduce costs in the well-planning, drilling, and production processes.
With HEAVY.AI, operators can visualize, cross-filter, and interact with these massive Telco and Oil & Gas datasets to deliver transformative efficiency. With millisecond querying, filtering, and visualization, the HEAVY.AI platform provides operators with instant insights. With HEAVY.AI’s sophisticated trend analysis, pattern recognition, and cross functional data integration capabilities, data scientists and administrators can visually detect equipment anomalies and patterns, predict failures before they occur, and perform corrective maintenance at the most efficient moment.