Supply Chain Optimization
Supply Chain Optimization Definition
Supply chain optimization refers to the tools and processes by which manufacturing and distribution supply chain performance and efficiency are improved, taking into account all constraints. Supply chain network optimization technologies use sophisticated algorithms and analytics to balance supply and demand in such a manner that sufficient raw materials are procured for manufacturing and distribution to meet customer expectations at the highest cost efficiency.
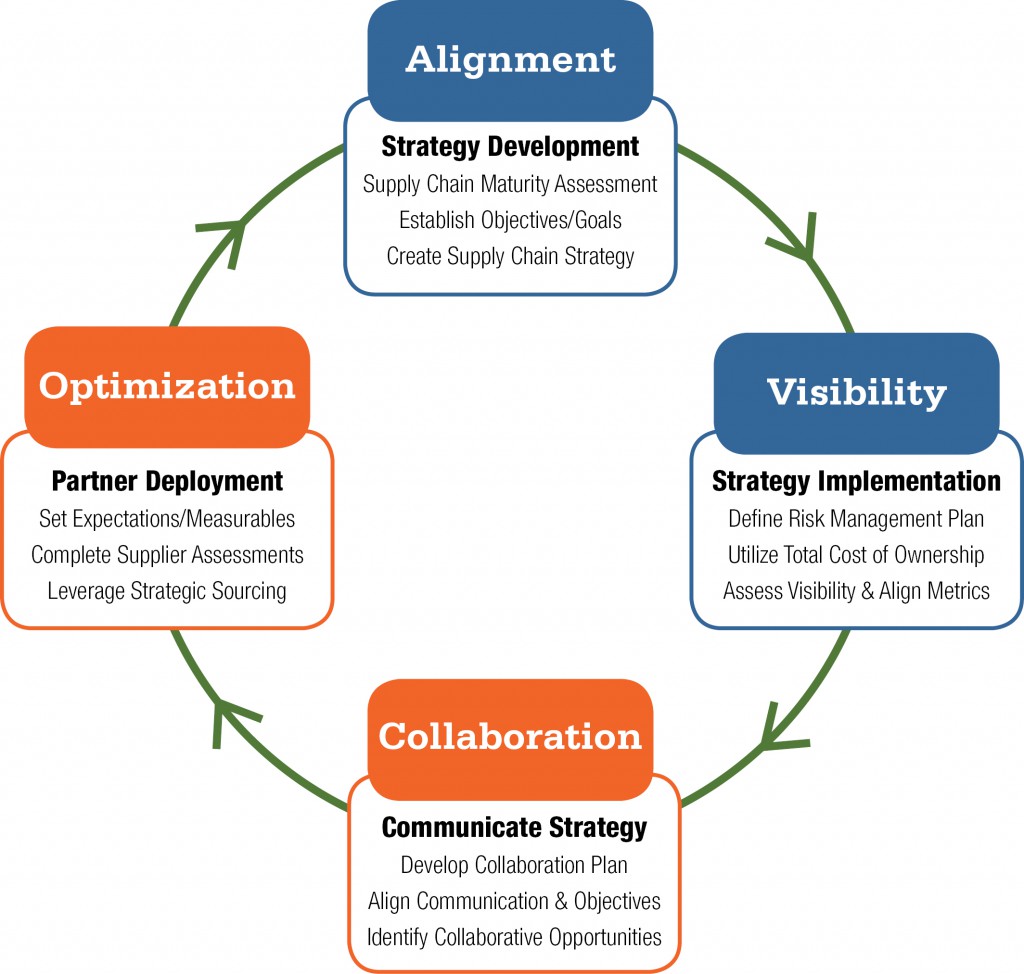
FAQs
What is Supply Chain Optimization?
A supply chain is a network of organizations, individuals, activities, information, and resources involved in the production and sale of a service or product to consumers. The chain begins with the transformation of natural, raw resources and components into a finished product or service, and concludes with the delivery of that product or service to the end customer.
The supply chain network design and optimization process enables businesses to maximize gross profits, minimize operating expenses, and ultimately create a successful customer experience that provides customers what they want, when they want it, where they want it, and at the lowest cost and highest profit, balancing the costs of distribution, inventory, manufacturing, and transportation.
How to Optimize a Supply Chain Network
Logistics and supply chain optimization is achieved with the use of sophisticated analytics and statistical software, which uses historical customer demand data in order to predict future inventory demand with the highest rate of accuracy. Supply chain inventory optimization results in an inventory level that is known as “model stock.” The forecast demand is used to develop a supply-chain manufacturing and distribution management strategy, which typically includes the following phases:
- Supply chain design optimization: focuses on warehouse locations, product flows within the warehouse facilities network, manufacturing schedules, and demand planning
- Supply chain planning optimization: determines how to manufacture and distribute products and/or services in a way that will balance supply and demand, and meet the forecast demand at the highest profitability
- Supply chain execution optimization: focuses on global trade management, inventory management, order management systems, real-time decision support, supply chain visibility, and transportation management
Supply chain optimization software solutions are capable of forecasting, balancing supply and demand, organizing and managing inventory and deliveries, and managing supply chain design, supply chain planning systems, and execution on a granular level. Inventory and supply chain optimization solutions are integrated into replenishment systems distribution requirements planning in order to seamlessly and precisely maintain the model stock profile in real-time.
Supply chain network optimization tools include sophisticated optimization algorithms, which are capable of accounting for load and unloading rules, load stability regarding decreasing transportation costs, palletizing logic, stackability constraints, and warehouse efficiency. Standard Deviation and Mean Absolute Deviation techniques may be applied to determine the amount of additional stock that should be maintained in inventory to mitigate risk of material shortfalls caused by unpredictable demand.
Modern supply chain optimization technologies typically provide a platform on which supply chain managers and supply chain optimization analysts gain real-time end-to-end visibility of supply chain operations; standardize, synchronize, and automate business processes and execution; and leverage machine learning capabilities and AI for supply chain optimization.
Benefits of Supply Chain Optimization
Advantages of supply chain network architecture optimization may include:
- reduced surplus inventory
- lower logistics cost levels
- improved customer service due to better forecasting and improved availability
- reduced time to act on supply chain issues and respond to market disruptions
- simplified supplier onboarding and collaboration
- decreased lead times
- reduced time, total cost, and risk associated with qualifying and managing new suppliers
- better resiliency, agility, and predictability in mitigating risks and maintaining business continuity
Does HEAVY.AI Offer a Supply Chain Optimization Solution?
HEAVY.AI enables supply chain managers to visualize and interact with billions of rows of telematics and supply chain data in real-time. Analysts can isolate and hone in on operations data during moments of peak demand, cross-filter by actual available inventory, and interact with location data.
With HEAVY.AI’s immersive logistics analytics dashboard, supply needs can be forecast based on real-time demand data streaming from warehouse sensor data; operational risks can be mitigated by quickly identifying unplanned maintenance requirements; and routing can be optimized by comparing external GPS, weather, and road maintenance data with internal staffing levels and fleet schedule. Use cases include Military Analytics, Logistic Operations for Defense, and Shipping Fleet Management.